What is cover glass for electronic devices?
Cover glass for electronic devices, also known as a display window, is a screen which is applied over an LCD to protect the device.
Typically, cover glass is plastic.
This can also be glass – especially on large format information displays.
For example:
Like the ones you would find at a train or bus station.
Why do we need cover glass for electronic devices?
We use information displays in our everyday life.
Whether it’s a:
- Mobile phone
- TV screen
- Computer monitor
Every display has a cover glass or display window applied.
Almost every industry uses them, including:
- Consumer
- Automotive
- Aerospace
- Marine
- Medical
- Industrial and so on
Generally, most devices will need protection.
On a day-to-day basis, these electronics will encounter varying environments which can affect their performance.
This means the cover glass will need extra enhancements to protect it and to help the consumer when they’re using it.
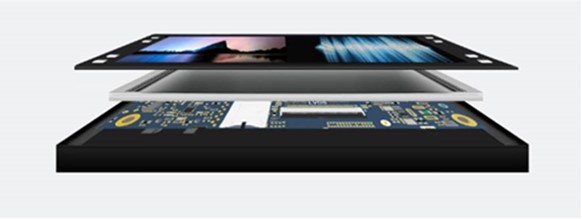
There are lots of different treatments available to help improve the performance of the cover glass.
They include:
- Environmental protection
- Increased lifespan and performance
- Abrasion and chemical resistance
- Reflection control
- Increased optical clarity
- Rigidity and durability
What protection/enhancement treatments are available for cover glass?
Anti-Reflection
A gloss surface treatment – Available in vacuum, wet & optical lamination application.
Designed to remove white light reflections from the device to aid the viewers experience.
Mainly for acrylic, but optical lamination is available on polycarbonate and glass too.
Reflection Control
A non-glare/matt finish – Part of the Optiguard™ range.
The coating applied in a liquid form via a spray method and cured using UV energy.
Intended to scatter/diffuse light across the display to eliminate reflections.
Also has added benefits of chemical and abrasion resistance.
Application for plastics.
Chemical & Abrasion Resistance
Clear gloss finish – Also part of the Optiguard™ range.
Applied in a liquid form via a spray method and cured using UV energy.
Used to offer greater abrasion resistance to plastics.
It allows the material to be used in a wider variety of applications.
Also available in non-glare/matt finish (See Reflection Control above)
Combined AR/Non-Glare
Fine non-glare/matt finish.
Vacuum deposited anti-reflection coating applied to both surfaces, combined with a single sided anti-glare (textured) coating applied to the front face.
Designed to distribute surface reflections, increase readability and give a softer image of the display.
Available on acrylic only.
Exterior Grade
Gloss Finish – Originally developed for vehicle headlamps, this treatment has excellent weatherability.
Only available for application to polycarbonate sheets and mouldings.
When applied to clear sheets, it’s been proven to increase the transmission of the polycarbonate.
Not only can you add different surface treatments to the cover glass to improve its performance, you can also manipulate it’s shape by CNC machining to shape or adding cut outs and cosmetic features such as screen printed detail to the face.
For example:
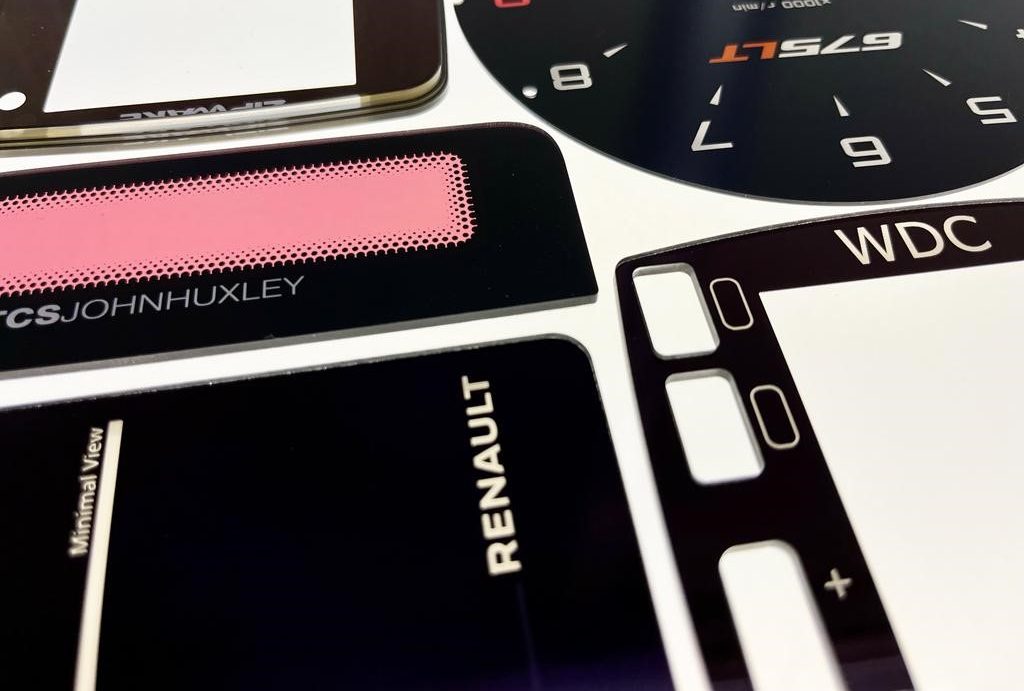
Available services for cover glass
CNC Machined to size
Taken from a master sheet size (Typically 1 x 1.5m) and converted into the finished part as per customer requirements. The surface can also have milled sections and cut outs in the profile.
Find out more about CNC machining.
Surface treatments
As explained above, we can apply our enhancement treatments/surface coatings to plastics to improve performance.
Find out more about surface treatments.
Assembly
Using our cleanrooms, we bond our cover glass to customer sensors, or LCD’s.
Find out more about our assembly process.
Gasket & Seals
Plotter cut 3M adhesives are applied to the plastics to aid final assembly. However, sometimes a VHB is used to seal the product and make it air tight.
Find out more about plastic fabrication.
Printed detail
Inks can be applied (Digital, screen, pad) to the surface to add customer logo’s and other details required for the cover.
Find out more about printing detail.
Got a minute?
Watch the below video to get more detail about the services we can offer:
Thank you for reading about cover glass for electronic devices. If you would like further information, please feel free to get in touch.